Why is calibration important? And how to deliver calibration services efficiently
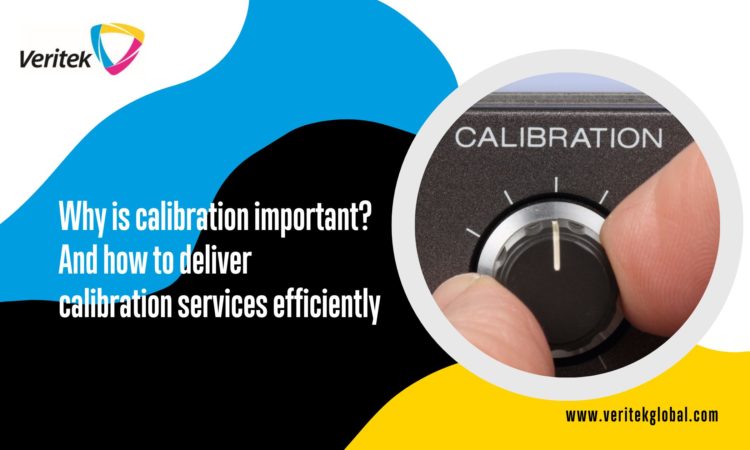
If customers rely on your machinery to deliver high accuracy and consistent performance, you’ll want to include calibration in your after-sales services.
Think about this for a moment. Calibration ensures equipment functions within your (the manufacturer’s) specifications, produces consistent results and complies with regulations and industry standards.
But here’s the thing: Although calibration is predictable and repeatable, the service is time-consuming.
Learn what calibration services involve and how to provide them efficiently and cost-effectively while ensuring customer satisfaction.
What is calibration?
Calibration is a preventative maintenance function that involves comparing the readings of a measuring instrument against a known standard or reference and adjusting the instrument if necessary to ensure its accuracy.
Why is regular calibration necessary?
Performance can gradually degrade when machinery operates over long hours and delivers high-volume output. This degradation is called drift.
When drift happens, results and output become unreliable, and production quality suffers.
To prevent drift from happening, calibration:
- Maintains accuracy: Tests to ensure precision and accuracy.
- Maintains consistent output quality: Tests to ensure equipment functions correctly and helps identify potential issues early.
- Reduces waste: Less waste keeps your customer’s costs down and increases machinery ROI.
- Reduces downtime: Helps technicians quickly identify sources of problems and make necessary repairs.
- Extends equipment life: When equipment operates within its designed specifications, wear and tear on components is reduced, resulting in increased reliability and longevity.
How does calibration work?
The calibration process typically involves using specialised equipment to compare a machine’s readings against a known standard or reference. Technicians then adjust the machine’s settings or components based on the calibration results to ensure it operates accurately.
Examples of calibration across sectors
Let’s take a closer look at what accurate and consistent performance means for our customers:
Printing presses
Regular calibration reduces waste, improves colour accuracy, and increases the productivity of the printing process. Most importantly, calibration ensures the production of high-quality printed materials that meet end-customer specifications.
Medical devices
Healthcare workers rely on medical devices to diagnose, monitor and treat patients. Regular calibration ensures accurate and reliable readings and effective treatment.
Digital cinema projectors
A drift in colour can make images look washed out, overly bright, or dark. Worse still, the scale of digital cinema screens magnifies colour drifts and detracts from a movie’s visual impact. Regular calibration ensures digital cinema projectors display movies accurately and consistently and audiences get a high-quality viewing experience.
Robots
Regular calibration ensures robot sensors accurately measure position, orientation, and other variables, ensuring robots perform tasks precisely and consistently. Calibration also helps to ensure the correct position and alignment of a robot’s actuators, reducing the risk of collisions, errors, and other problems.
How a third party can help OEMs deliver calibration services
As mentioned before, calibration is predictable, repeatable, low-risk and time-consuming. For this reason, third parties can provide a valuable resource for OEMs because of the following:
Access to advanced equipment: Third-party calibration service providers invest in the latest and most advanced calibration equipment and tools, which may be uneconomical for OEMs to purchase and maintain themselves.
Technical expertise: Third-party calibration service providers employ OEM-trained technicians with the knowledge and expertise to calibrate many equipment types and models, ensuring best-practice calibration.
Economies of scale: Access to advanced equipment and technical expertise means that partnering with a third party can be more cost-effective than investing in in-house equipment, personnel, and training.
Compliance with standards: Calibration is critical for compliance with regulatory standards such as ISO and other industry-specific requirements. Third-party calibration providers have experience with these standards and can help OEMs ensure compliance.
Faster turnaround times: Because third-party calibration service providers have a workforce dedicated to delivering calibration services, OEMs can expect faster turnaround times.
To sum up
Calibration is an essential preventative maintenance task that ensures OEMs’ products operate reliably and reduces the risk of downtime.
The good news is that delivering calibration services doesn’t have to be down to you.
Because calibration is predictable, repeatable, low-risk and time-consuming, a third party with the right equipment and technical expertise can be a beneficial resource for OEMs.
With a third party’s help, an OEM providing calibration as part of their after-sales service package can benefit from economies of scale, compliance with standards, and faster turnaround times.
We’re ready. Are you ready to find out more?
This blog is relevant to the following Veritek industry sector verticals:
Medical
Robotics and cobotics
Print & Graphics
Optometry
Digital Cinema
Photo imaging