7 reasons why you shouldn’t neglect planned preventative maintenance
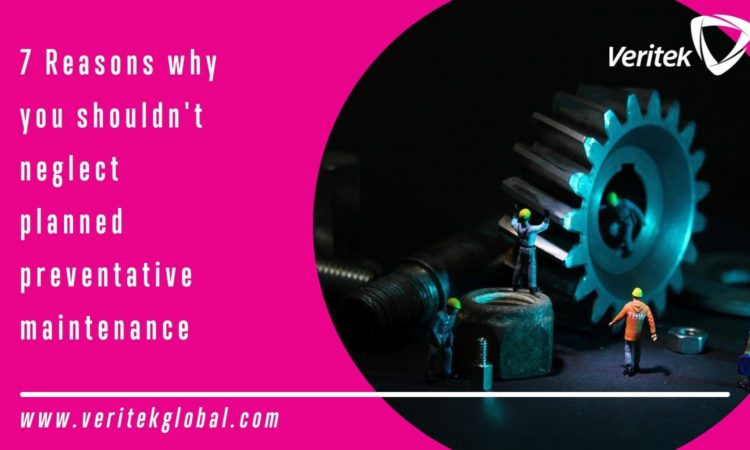
"You wouldn't jump out of an aeroplane without having a system to perform regular inspections on all the components that make up your sky diving kit. Because you know, regular checks protect you from potentially dangerous situations."
“You’re calling to book in planned preventative maintenance? I’m too busy. Call me back in a month.”
“We don’t need planned preventative maintenance right now. We’re happy with the way our equipment works.”
Advocating for the value of carrying out planned preventative maintenance is a daily task for Veritek’s Customer Service team.
Yet the notion of delaying planned preventative maintenance surprises our Veritek Field Engineers.
As they put it, “You wouldn’t jump out of an aeroplane without having a system to perform regular inspections on all the components that make up your sky diving kit. Because you know, regular checks protect you from potentially dangerous situations.”
Safety is one reason planned preventative maintenance is essential for businesses that operate mission-critical equipment.
Beyond safety, companies should be aware of other strategic reasons to prioritise planned preventative maintenance.
Before I go any further, let me explain what planned preventative maintenance is.
What is ‘planned preventative maintenance’?
Planned preventative maintenance is a regularly scheduled inspection of a business asset or a range of assets across an estate.
The rationale for planned preventative maintenance is prevention is better than cure. You see, regular inspections catch problems before they arise.
Here are seven additional strategic reasons to prioritise planned preventative maintenance (PPM) and make it part of your business routine.
1. PPM dramatically reduces the risk of business disruption
When you regularly schedule preventative maintenance, you turn it into a habit.
Better still, you can schedule preventative maintenance at a time that causes minimum interruption to business activities.
2. PPM reduces downtime
Unplanned downtime can cripple unprepared businesses. If breakdowns bring productivity to an unexpected halt, businesses can miss vital deadlines, lose out on opportunities, and have damage inflicted on their brands and reputation.
Regular preventative maintenance reduces potential problems before they cause costly interruptions to company operations.
3. PPM prevents costly repairs
Unplanned maintenance requires an emergency engineer call-out, parts and downtime.
These costs affect the bottom line because emergency repairs cost an estimated three to five times more than planned maintenance.
On the flip side, planned preventative maintenance lets you accurately budget and spread maintenance and associated costs evenly throughout the year.
5. PPM prolongs the life of your equipment
You can expect a longer lifespan and a lower total cost of ownership from regularly and well-maintained equipment, leading to a better return on investment.
6. PPM maintains the accuracy and quality of output
Costs associated with poor quality output include product waste, energy waste, missed customer deadlines, warranty claims and potential product recall.
If you operate in a competitive market, planned preventative maintenance can help you maintain accuracy and quality of output.
7. PPM reduces energy consumption
Poorly maintained equipment assets tend to use more energy than regularly maintained equipment.
Consequently, planned preventative maintenance helps companies lower energy bills.
8. PPM improves customer experience and satisfaction
For OEMs, having the capacity to provide planned preventative maintenance is expensive.
Fortunately, there is a solution. An after-sales support package from a field engineering support partner, such as Veritek, provides a cost-effective way for OEMs to enhance customer experience and satisfaction.
Conclusion
Unplanned breakdowns cause costly business disruption, including crippling downtime and costly repairs.
When you make planned preventative maintenance part of your routine, you can budget more effectively and rely on more predictable cashflow.
After that, planned preventative maintenance helps you get maximum ROI from business assets by ensuring accuracy and quality of output and prolonging asset lifespans.
Elsewhere, planned preventative maintenance helps reduce energy consumption and associated costs.
Finally, planned preventative maintenance helps OEMs anticipate and respond to customer service and support requests, increasing customer satisfaction.
Can you really afford not to get a planned preventative maintenance appointment scheduled in your diary?
This blog is relevant to the following Veritek industry sector verticals:
Want to discuss your needs?
During the call, we’ll discuss the support you need and whether our third-party service partnerships would be a good fit for your OEM service division.
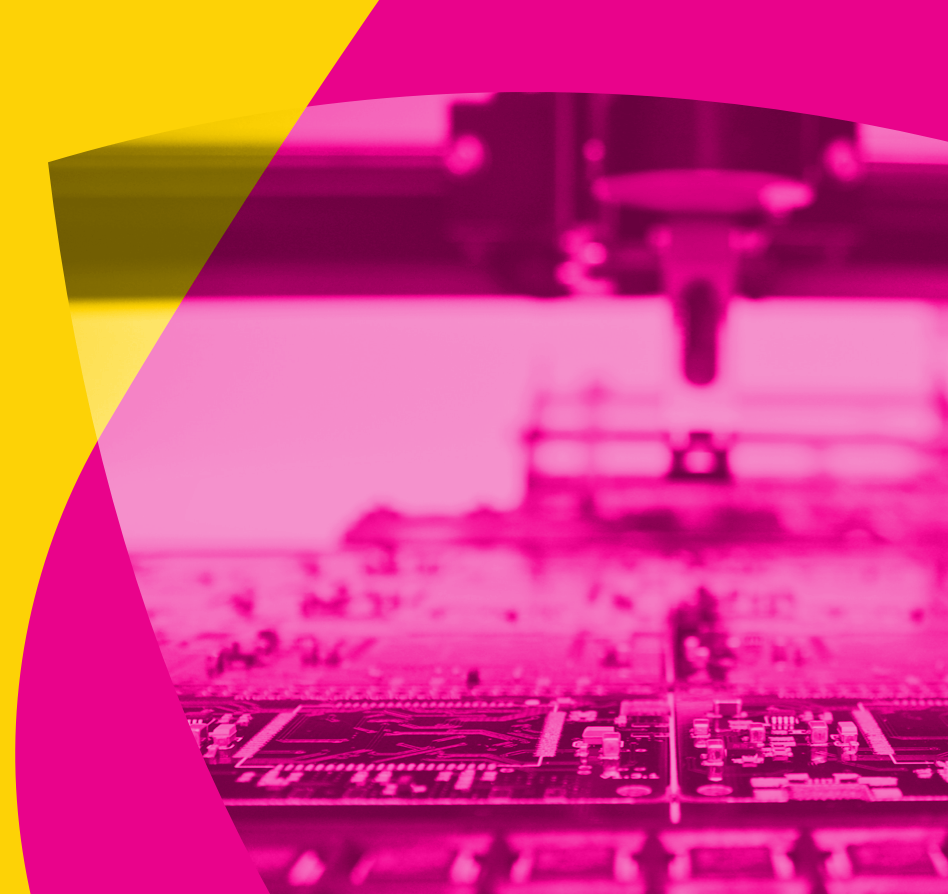