Strategies Service Managers Use To Manage Unpredictable Workloads Caused By Mechanical or Software Upgrades
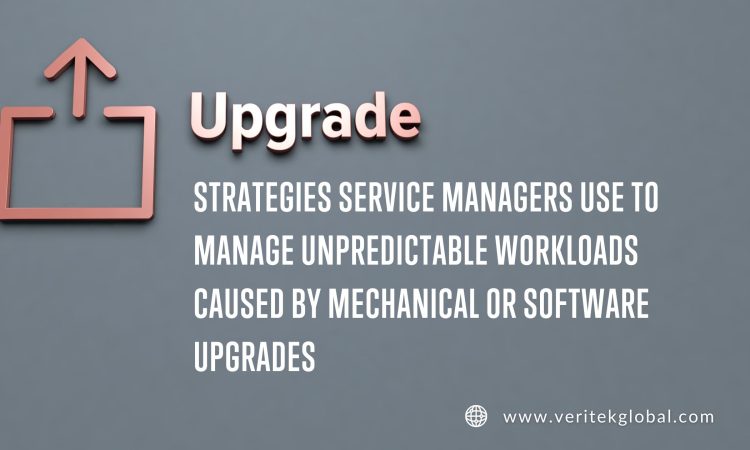
As a Service Manager working for an Original Equipment Manufacturer (OEM), you know the constant balancing act required to maintain smooth operations. Our customers tell us one of their most pressing concerns is managing increased and unpredictable workloads, especially when introducing additional volumes such as mechanical or software upgrades.
Our customer base comprises service managers for world-class OEMs. Here are some techniques they tell us they use to manage unplannable peaks in demand without compromising on other essential maintenance activities.
The Challenge: Balancing Unpredictable Workloads with Ongoing Maintenance
Introducing new software upgrades or mechanical enhancements is crucial for staying competitive.
Experienced service managers plan and budget for upgrades to avoid significantly draining resources and pulling engineers away from planned maintenance tasks. To plan for unpredictable workload increases, they consider:
Ensuring continuity of operations
They know they must maintain the service levels their customers expect.
So, when they divert engineers to upgrade projects, they ensure they pay attention to routine maintenance and other critical tasks.
Flexibility and scalability
They enhance the use of engineers to prevent potential delays from increased workloads. However, they recognise that there are more sustainable long-term solutions than this approach.
Cost efficiency
OEMs provide essential services to their customers. Experienced service managers ensure these services are cost-effective, scalable, and flexible. They strategically plan for increased workloads, allocating resources efficiently to minimise excessive overtime costs.
Maintaining Service Quality and Customer Satisfaction
They maintain high service quality during significant projects, which can take time and effort, with limited resources.
Strategic Resource Planning: The Key to Success
When dealing with unpredictable workloads, such as mechanical or software upgrades, experienced service managers excel in strategic resource planning.
They expect the unexpected and plan for the unplannable, preparing for unforeseen yet foreseeable events.
The challenge lies in the timing, as it is often unpredictable. This type of planning is akin to developing a business continuity plan.
Experienced service managers incorporate cost-effective flexibility into their resource allocation and activities. They balance budgeting for anticipated events with avoiding underutilised resources while waiting for these events to occur.
In particular, experienced service managers do the following:
Prioritise Preventative Maintenance: They plan a window for routine maintenance and create flexibility to help optimise resource reactions.
Optimise Engineer Utilisation: They meticulously plan their workforce schedule and engineering coverage to balance new upgrade projects and routine maintenance. Good scheduling software helps service managers optimise engineer time, ensuring critical maintenance is not deferred.
Remote support: They always look to optimise the use of remote support to increase efficiencies, provide scale for their operations across geographic boundaries, and effectively provide a fast response time.
Build in Strategic flexibility: Knowing that there will be unpredictable peaks in resource demand to react to, service managers build into their planned activities resources that can be scaled up when the peaks arrive. Because they are part of the day-to-day activity, service managers can quickly deploy these resources.
To sum up
We see a big difference in OEM service organisations that can plan strategically to be ready for something they know will happen but don’t know when compared to those that don’t.
Those able to plan this way for unplanned, unscheduled and unpredictable events such as mechanical or equipment upgrades can maintain their ability to provide continuity of customer service through events. We see this has a long-term positive impact on Customer Satisfaction.