Why should break/fix support form part of your equipment maintenance strategy?
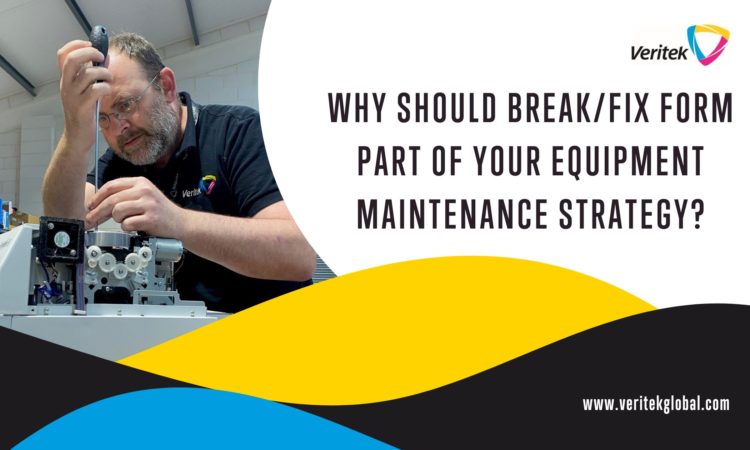
It’s a question customers often ask. But the simple fact is this. While predictive sensors and warning systems make machinery more reliable by predicting issues, they cannot physically resolve problems. This is why break/fix support is essential to any service division’s maintenance strategy.
In this post, we explain what a comprehensive maintenance strategy includes and how to incorporate unplanned break/fix support most cost-effectively.
What is a comprehensive maintenance programme?
A comprehensive maintenance programme aims to reduce downtime, minimise repair time when problems occur, and extend equipment life.
Where does predictive maintenance fit in?
Predictive maintenance involves continuously monitoring the performance and condition of mission-critical machinery using sensors, software, and other technologies. Data is analysed to identify patterns and trends predicting when equipment will likely need attention. After that, warning lights or messages alert users to machinery maintenance needs. It aims to identify potential problems before they become issues and prompt action to reduce the likelihood of unexpected downtime.
Where does preventative maintenance fit in?
Preventative maintenance is another form of predictive maintenance that aims to detect and fix potential issues before they become significant problems.
Whereas predictive maintenance uses sensors to detect problems, preventative maintenance is regular and scheduled.
What is break/fix support?
Break/fix support refers to a technical support service that depending on the nature of the problem and the type of equipment involved, an OEM-trained technician is called upon to:
- Provide remote machinery support
- Provide onsite field engineering support
In contrast to predictive and preventative maintenance, break/fix support is reactive as it requires the technician to understand the root causes of issues and fix them.
Remote and onsite break/fix services aim to restore mission-critical equipment to full operation as soon as possible to minimise downtime and production interruptions.
Where does break/fix support fit into a modern maintenance strategy?
As mentioned above, while sensors and warning systems can alert users to potential issues, they cannot actually carry out repairs.
Therefore, when predictive or preventative maintenance prompts action, break/fix technicians interpret sensor messages, diagnose the problem, make necessary repairs, replace parts and calibrate machinery when needed.
Why mission-critical equipment needs technical support
When uptime is crucial
Mission-critical machinery often operates in high-stress conditions, and end users cannot afford downtime.
When factors beyond OEM’s control cause unplanned downtime
Even if mission-critical equipment is well designed and regularly maintained, it can still need technical support due to unforeseen circumstances such as:
- Human error: Equipment can break down due to incorrect usage, accidental damage, or lack of proper user training.
- Power issues: Power surges, voltage fluctuations, or power outages can cause equipment to break down.
- Environmental factors: Exposure to extreme temperatures, dust, moisture, or other environmental factors can cause equipment to malfunction.
How to plan for break/fix support calls
While manufacturers and third-party channel partners typically offer break/fix services, they tend to need more time to plan for because of the unpredictability of the calls.
In these cases, a third-party service provider such as Veritek can supplement an OEM’s team with highly skilled remote support and field engineers when needed.
You see, when you enter into a service partnership with Veritek and train its engineers on your products, you can call upon Veritek engineers at short notice for unplanned or time-limited projects, making a break/fix service partnership the cost-effective choice.
In summary
IIoT is revolutionising how companies maintain equipment.
Predictive maintenance provides valuable insights into potential issues and, together with preventative maintenance, makes mission-critical equipment more reliable by alerting users before they become problems.
Because sensors cannot physically fix problems, break/fix technicians use their technical knowledge to identify the root cause of a problem and determine the most appropriate response.
Sometimes they need to physically repair or replace worn parts. Other times they need to calibrate machinery.
The need for reactive break/fix support is pretty obvious once you think about it.
Do you agree? I’d love to know your thoughts.
This blog is relevant to the following Veritek industry sector verticals:
Medical
Robotics and cobotics
Print & Graphics
Optometry
Digital Cinema
Photo imaging
Want to discuss your needs?
During the call, we’ll discuss the support you need and whether our third-party service partnerships would be a good fit for your OEM service division.
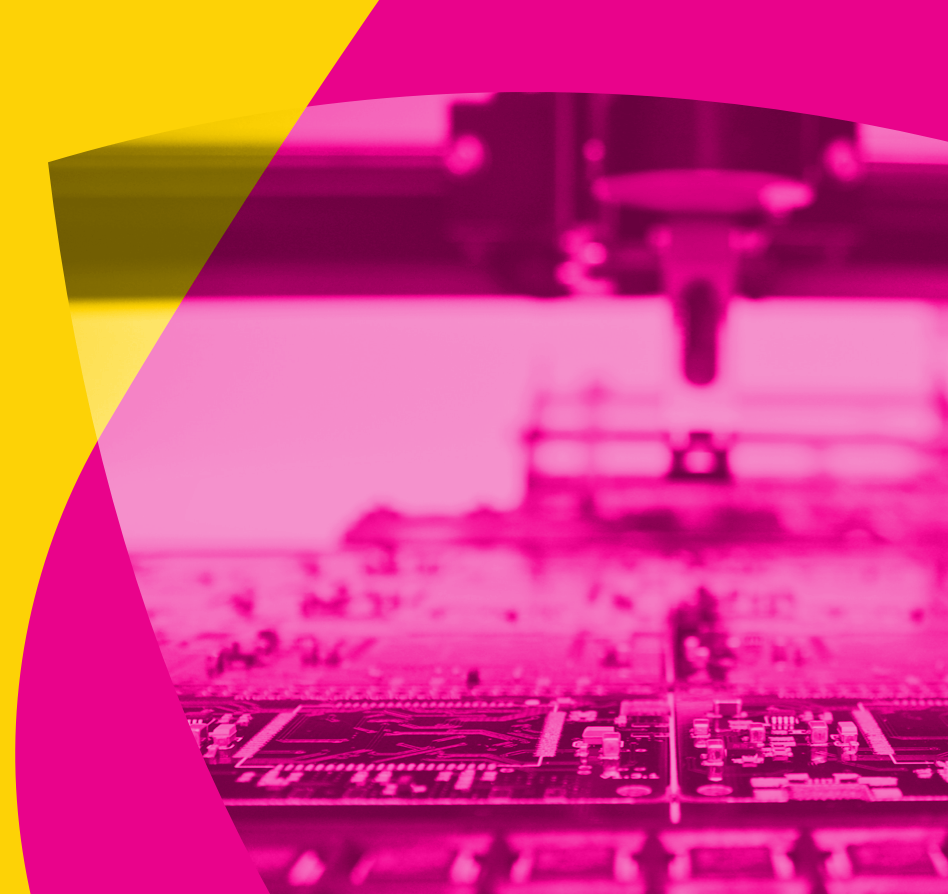